Belt-drive motorcycles are nothing new. Although some motorcycles in the early 1900s had already adopted chain drive, many had not, and museums around the world are replete with old motorcycles wearing leather or reinforced rubber belt-drive systems.
In the bad old days, these primitive systems were not much of a problem, since power output from the contemporary engines was, to say the least, modest. By about 1912, as engine output climbed, even those motorcycle manufacturers which had been using belts switched to chains, or-in a few cases-to shaft drive.
At the time, this made sense. After all, engine development was proceeding faster than belt-material technology. But belt design continued to improve, driven largely by industrial applications as well as in automotive auxiliary systems like fan belts and cam drives. Much improved by new rubber and cord formulations, belts eventually reappeared as a motorcycle final drive on cruisers, notably on the Harley-Davidson FXB Sturgis of 1980.
The enabling technology was a DuPont Kevlar formulation used in what belt manufacturers call the “tensile members”, or cords within the rubber belt that provide the necessary strength and stretch resistance. The rest, as they say, is history, and cruisers these days are more likely to feature belt drive than not.
Long after we’d become accustomed to seeing belts on cruisers, something surprising happened. BMW opted for belt drive on its new F800 series of sport twins, followed shortly by Buell, with its new 1125R sportbike. Buell, with its long association with Harley-Davidson and that company’s engines, already had experience with belts on some of its models and was perhaps more inclined to look at belt drive on sport machines, but the BMW was a real surprise. Nonetheless, I suspect the reasoning was similar.
Belts are lighter than chains, and help reduce unsprung mass at the rear wheel. Roller chain suspended between the countershaft and rear sprockets has more wrap at the rear wheel, and thus places more of its weight there. Unsprung mass is one of Erik Buell’s major preoccupations, and he does his utmost to reduce it.
But low mass is not the belt’s only virtue. Belts are quieter, do not rust, resist environmental pollutants and require no lubrication. Anyone who has cleaned oil splatter off the rear wheel, swing arm and suspension pieces of a motorcycle will attest to the value of that. And even though motorcyclists are more inclined to increase noise from their mount, usually by fitting a loud pipe, there’s something to be said for a reduction in driveline noise.
A typical, contemporary belt is made up of a synthetic rubber envelope containing an aramid cord structure, with a high-modulus rubber material (called tooth stock) making up the rectangular teeth that conform to their mirror image on the drive pulleys. Veyance (manufacturer and marketer of Goodyear Engineered Products, including motorcycle drive belts) calls the tensile-member material Flexten, and it is a multi-filament helical weave that is looped endlessly around the belt circumference much like we see in modern tire construction.
One of Veyance’s particular techniques is to encapsulate each bundle of filaments in an adhesive material to minimize friction and abrasion between the bundles as the belt goes about its business. The tooth side of the belt is finished in what’s called facing material, and this is an important part of the belt because this is what makes contact with the pulleys.
A degree of compliance is required for perfect conformity to the pulley profile as well as considerable abrasion resistance. According to Veyance motorcycle project engineer Brian Wegele, who worked closely with Buell on the 1125R project, his company’s facing material uses an alloy of polyethylene and EPDM synthetic rubber cross linked by vulcanization.
Much of the development work for facing material was done for NASCAR cam-drive belts, and as a consequence the material can withstand operating temperatures of 300 degrees — probably a bit warmer than it will get on the back of your bike.
An intrinsic property of aramid cord is that it does not stretch. So there’s no need to incorporate axle adjusters on a motorcycle, nor suffer the alignment challenges that come with them. Because the swingarm and drive pulleys are at different distances from the rear axle on motorcycles, producing unequal radii when the bike’s suspension deflects, belts and chains both need some play to accommodate the variation in length.
On chain-driven bikes we just leave some slack, but belt-drive bikes can exploit more elegant solutions. Such as the tensioner wheel seen on Buell’s 1125R, which is loaded against the belt and visibly rotates backwards as the bike rolls along. This system takes up slack, helping to eliminate the driveline jolt or shuffle one often experiences when you open the throttle on a chain-driven bike.
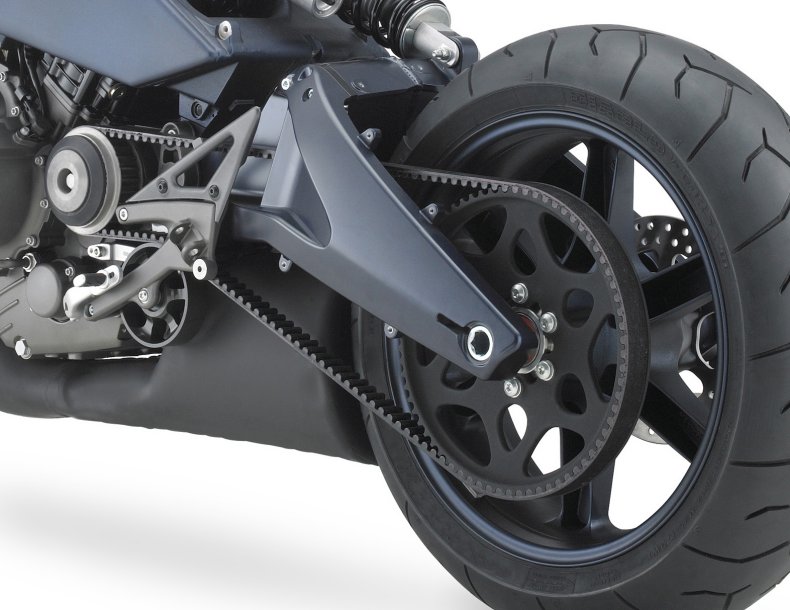
BUELL BELT DRIVE SYSTEM
There’s inertial mass to consider with chains, too. Just as it requires energy to accelerate the rear wheel, so it does to accelerate the hefty mass of metal that makes up your typical chain. Still, some of you are doubtless thinking that belt drive can’t match chain when it comes to high-power applications, right? Actually, they can. One might have to widen the belt somewhat to handle serious horsepower, but the material has remarkable strength. Aramid on a per-pound basis is stronger than steel.
According to Wegele, Veyance has broken a new chain at 8,000lbs/strand compared with their Flexten material at 9,000 lbs/strand. And the company is researching carbon fiber tensile members that require 11,000 lbs/strand to reach the failure mode. There is, according to Wegele, no reason that belt-drive cannot be used on modern sportbikes of any displacement.
The technology is already being pushed by escalating power and weight in the cruiser segment, and Wegele is confident that Veyance can meet any power transmission challenge. He says that even the fatigue and failure characteristics of belts are benign. Typically, he says, a belt will exhibit terminal wear problems on a “limp-home” basis rather than a “walk-home” one. Belts will usually lose teeth and provide palpable evidence of their distress well before a catastrophic failure occurs. Moreover, belts do not damage their pulleys in the way chain distorts tooth profiles on a sprocket.
Observant readers might recall that a Buell 1125R racing in the Daytona 200 retired because of belt problems, but Buell spokesmen point out that the bike was racing without the usual belt covers. They say that rubber residue from the track was flung from the tire onto the pulley’s edge where it gradually built up until it began pushing the belt sideways off its track. The belt itself was fine, there was just a danger of derailment.
But racing is perhaps the only environment that does not favor the belt, and that’s primarily because racers need quick final-drive ratio changes. Belts can’t be broken and then riveted back together again, so their lengths are unchangeable. To alter ratios you need to carry pulleys and belts of varying length. It’s not impossible, just inconvenient. Since most production sportbikes are chain driven anyway, it’s not a problem that will arise until more manufacturers switch to belts. If they do.
Thus, racing applications for belts are now pretty much limited to blowers and primary drives. Oh, and to the occasional Buell. The endless aspect of belt construction poses a few challenges for belt replacement, since-unlike chains-they cannot be cut and rejoined, but that’s something that can be taken into account during the motorcycle’s design stage.
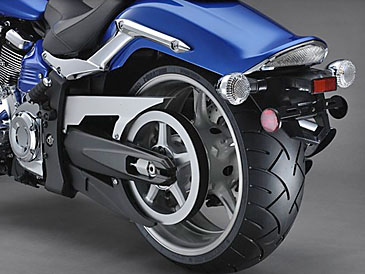
Star Raider Reliably Puts Big Torque Through a Relatively Narrow Belt
None of this suggests that chains will disappear anytime soon. For one thing, chain can wrap around smaller sprockets than can belt. Chain will happily embrace chain wheels down at about 3-inches in diameter, whereas belts need pulley diameters of at least 4.5-inches if they are not to begin feeling distressed. And because the countershaft pulley is big, so must the wheel pulley enlarge in order to get the appropriate final-drive ratio. Some people may not like the appearance of a big belt pulley on the rear wheel. Chains are narrower than belts too, and because they straddle the sprockets, produce a pretty narrow total package.
There have been pretty impressive improvements in chain technology, as well. Improved metallurgy has led to higher tensile strengths, while modern manufacturing processes have improved tolerances and assembly techniques. The biggest bugaboo with chains is that they are not flexible. Instead, individual links are allowed to pivot on bushings at both ends of every link. The challenge has been to defeat the wear that occurs at the moving elements that allows longitudinal play. The play permits the chain to stretch beyond its operating limits, to the point where its combined link pitch no longer matches that of the polygonal sprockets on which it rides.
Efficient lubrication reduces the wear, but external oiling can only go so far in mitigating bushing wear, so manufacturers came up with the clever idea of packing grease inside the bushings, and then sealing the end plates (which move in relation to each other) with O-rings. That dramatically increased the service life of chains, but we soon found that the O-rings were susceptible to wear and environmental attack from aggressive cleaning materials or from the solvents in inappropriate lubricants.
But most consumers have caught on now, and ensure that chain lube containers indicate the formulation is suitable for use with rubber O-rings. Now we are seeing variations on the O-ring theme, with X-rings that offer multiple lubrication pools and seal points, and from chain manufacturer RK Chains, a novel new twist called the XW-ring.
This page from the manufacturer’s website probably explains it more clearly than we could. Note that the text here contains RK’s claims, unverified by MD
Obviously, chain manufacturers are not about to give up their huge involvement with motorcycles. Nor should they. But it’s nice to see an alternative to the noise and mess of chains, and the extra unsprung weight of shaft drive. Right now, belt-drive has made huge inroads into the cruiser market. The big question is how far the technology may penetrate the rest of the motorcycle model spread. It’s going to be an interesting tug-of-war.