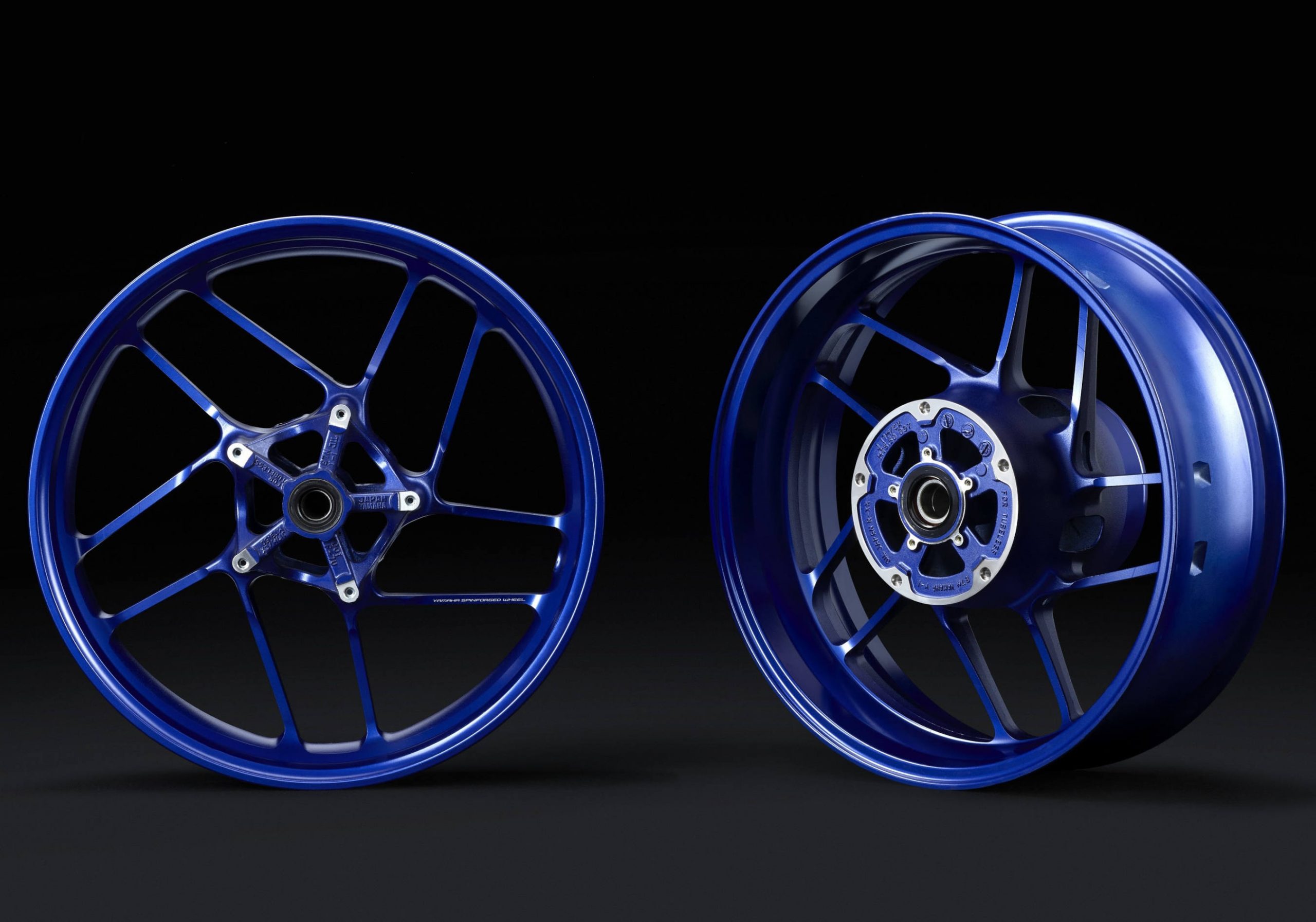
You might be surprised that even some of the larger motorcycle manufacturers outsource a number of parts in their motorcycles to third party venders. Yamaha has a proud tradition of casting and forging aluminum parts in-house, and has developed several innovative techniques to improve the strength, and reduce the weight, of certain parts, including wheels.
The recent introduction of the redesigned 2021 MT-09 mentioned that the wheels were SpinForged, a process developed by Yamaha that results in rim thickness reduced from 3.5mm to 2mm. This new process is described in the following press release from Yamaha, and the video embedded below:
An aluminium “bartender” whose work led to lighter weight
Developed for the all-new 2021 MT-09 motorcycle, Yamaha’s SpinForged Wheels established a new and innovative way to reduce weight through the flow forming process they are manufactured with. One of the key drivers that led to the successful application of this method with a mass-production motorcycle for the first time in the world was the development of a special aluminium alloy tailored specifically for flow forming by Yamaha’s in-house materials research departments. In this issue, we introduce the aluminium specialist at Yamaha who played a central role in the development process for creating these new lightweight wheels and some of the challenges she faced.
Harnessing the talent of an aluminium research specialist
“Just changing a few conditions can completely alter how aluminium reacts, or its ‘personality’ so to speak,” says Kahori Oshima of Yamaha Motor’s Materials Division. She speaks of the metal as if gleefully introducing a friend or close acquaintance. “It can be really sensitive sometimes, often giving us zero margin for adjustments.” Despite this “personality”, aluminium is an essential material used to create our motorcycles, outboard motors and various other Yamaha products.
Since joining the company, Oshima has worked as a materials researcher specialising in aluminium and her work and findings have won her praise and trust from Yamaha’s development and manufacturing arms. “She’s like a bartender for aluminium and her skills at making these ‘cocktails’ are something Yamaha is very proud of,” proclaims her superior.
Further, while the material itself may be spoken of as simply “aluminium”, what is required of the material can greatly differ depending on the product in question, where a part is to be used, and the machining method called for. “Yamaha has a massive collection of aluminium ‘recipes’ created by our predecessors and this is one of our strengths,” continues Oshima. “We have an ethos here of aluminium being an area of manufacturing that we must never be outclassed in, and I think what lies behind that is the fact that Yamaha has long done casting all on our own. That confidence and pride pushes us.“
Working with aluminium entails carefully controlling the temperature of the red-hot molten metal, mixing the secret blend of additional elements in, and then heat-treating the formed piece to finish it. Oshima’s task as a researcher is to call on her academic knowledge as well as apply new ideas to find the right balance of stiffness and flex while pursuing not only excellent overall strength and toughness but also beauty.
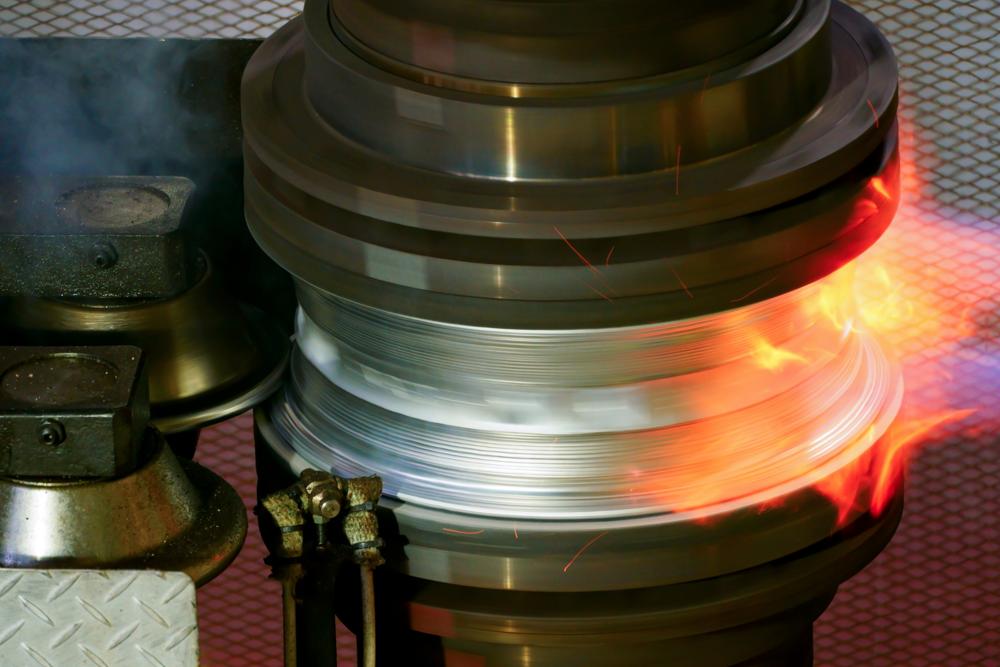
Innovations born on the factory floor
The new aluminium wheels fitted to the latest MT-09 are machined using flow forming and are a standout manifestation of Oshima’s research.
In developing this model, Yamaha embarked on a new and ambitious challenge of extreme weight reduction, driven by the idea that if you can somehow augment the base characteristics of the aluminium, it will spur new innovations to come from the factory floor itself. The engineering and manufacturing departments both threw themselves into the project and successfully created a special aluminium alloy and heat treatment process even their predecessors had yet to concoct. This combination enabled the company to offer the first mass-produced flow-formed motorcycle wheels. Naming them Yamaha SpinForged Wheels, each boasts rims just 2 mm thick (compared to 3.5 mm with the outgoing model) and the front and rear wheels together are some 0.7 kg lighter. Weight reduction is among the most challenging tasks in the industry and such a success makes these wheels worthy of being hailed as innovative.
“What we struggled with the most was having no metrics to go on. Without them for evaluation, we can’t figure out where we need to set our target, so it was certainly difficult to develop a material and build an appropriate method of evaluation at the same time,” confesses Oshima. However, the struggle and hard work made the achievement that much more rewarding and she has immense pride in these wheels.
“For example, if it’s strength alone, aluminium can’t beat iron. But on the other hand, aluminium has advantages like its lightness, corrosion resistance, high machinability and its beauty. Even if our Monozukuri changes in the future, I’m certain aluminium will remain a material of choice. I believe my role as a materials researcher is to extract and enhance that potential.”
Yamaha Motor’s casting journey
Our roots in casting technology lie in the techniques used to cast piano frames at Nippon Gakki Co., Ltd. (today’s Yamaha Corporation). Those techniques were adapted and applied towards creating the engine and parts for the first Yamaha motorcycle in 1955, the YA-1. Since then, Yamaha has continued to cast a plethora of parts not only for motorcycle engines but also for chassis, marine products, car engines and more – all in-house. The capability to cast both large and small parts and components in-house has made us a rarity among the world’s motorcycle manufacturers.
Producing the wheels for our motorcycles is a good example of this capability. In addition to vacuum die-casting aluminium wheels, Yamaha succeeded in casting magnesium wheels for mass production with the YZF-R1 in 2015, something once thought unfeasible for a high-volume product. The flow forming process for creating Yamaha SpinForged Wheels was also already often employed when producing wheels for cars, but motorcycle wheels require an appealing design on both sides, thus adapting flow forming for our industry presented high hurdles. To clear them, Yamaha carefully selected an aluminium variant to work with, conducted repeated experimentation of different alloy combinations in search of the right strength and lasting toughness, and devised the ideal heat treatment method to match. The Yamaha SpinForged Wheel was the result of this work and more.
Yamaha’s factories have given birth to numerous new technologies in the casting field, from our controlled fill (CF) aluminium die-casting technology capable of mass-producing large but thin parts to our all-aluminium DiASil Cylinder, a world first. These achievements underpin the deep and long-held pride the craftsmen at Yamaha’s worksites hold, believing the company’s aluminium casting expertise to be one of its greatest strengths and a field in which it must always be a leader.
I wonder if the guy at the dealership who’s changing a tire, unaware of the thinness of this wheel can break it with the changing machine tooling used? Its seems so thin that special tire changing techniques may be necessary?
I remember seeing Mission Tool do this in person for the Arlen Ness bikes back in the early nineties. I just assumed this was how all aluminum single-piece rims were made.
To me this just seems like a way to reduce production costs to increase profits. They just dressed it up with fancy words to make it seem like a wonderful new technology. Kawasaki has been producing ATV wheels used by other manufacturers for years. Just look for KMM stamped letters(Kawasaki Motors Manufacturing)
It reduces unsprung weight, which has benefits to everything from comfort to performance. If costs go down, its a win/win for riders and Yamaha. If these wheels are going to break Yamaha will be facing lawsuits, and Yamaha has a pretty impressive record of matallurgical innovations driving the industry forward. I think we have every reason to trust this isn’t some type of shrink-flation.
Spun aluminum has been around for decades and this method of producing wheels has just been evolving to a point where they feel it necessary to tout it as a new technology. 2mm is .080 or 5/64”. That is getting pretty thin for aluminum wheels that must live in an unpredictable environment which today’s poorly maintained roads certainly offer. The MT-09 will prove these wheels to be successful or not.
Well said. They can make aluminum stronger at the cost of embrittlement. At 2mm/0.080”, the crack risk goes up. I guess we’ll see what happens.
As dry as this sounds, and ignoring the atypical pride-flash from a Japanese person, this process is a big deal. It’s been used on aircraft for many years and is still very expensive compared to traditional methods.
Don’t discount the thin material as weak or easily bent, this process produces a much stronger product as compared to conventional methods of forging.
Also, don’t compare these light wheels with the magnesium wheels on the R1. Magnesium sacrifices strength for extreme weight savings but the material is soft and not good at taking abuse. They’re great on a track with few harsh bumps, but a terrible idea for the street.
Magnesium wheels? My ancient kz1000P has them.
Anyways, I mount and balance my own tires using seven inch long tire irons. And even those put a lot of stress on the wheel depending on which tires I use. I’d love lighter wheels on my bikes but not weaker ones. Sport touring tires are harder to mount than sport tires,
That’s a fact about sport touring tires. In fact, that’s what drove me to stop mounting my own tires by hand. I bent one wheel that way and knew I had to stop.
When I mount my tires I do both at the same time. I sometimes do it myself but usually I have my brother come by. An extra set of hands make this go way easier.
ST tires aren’t too bad, the stickier high performance ones anyway, like Dunlop Q3 and Q4 or even Bridgeston S22s. Race tires are super stiff carcasses and are as bad as mambo cruiser tires.
My No-Mar changer setup paid for itself in a year while I raced as I went through 15 tires that season (and I remounted the practice tires multiple times till they wore out). If I had spooned them on instead of using a mounting bar that spins it on, I’d have had to replace rims many times over.
These newer thinner rims might be fine on mounting machine like an automatic Coates over their useful life but for shops that still use spoons, that’s asking for trouble. And read the fine print if you take it somewhere…not responsible for rim damage!
It sounds like they start with a forging that they then machine and press and form to the dimensions desired, all while compensating adequately for the greater rigidity (density) of a forging as opposed to the relative ductility of a casting. I’ve always had a lot of respect for Yamaha. This is an astonishingly able company. Yamaha makes pianos and keyboards, brass instruments, audio equipment (I’ve had a receiver and CD player), motorcycles (I’ve had 3), and does engine building for Ford and Toyota on contract. That’s a pretty good resume. Actually, each of the Japanese Big Four is pretty cool and each has its own strengths but they also have no real weaknesses either.
That’s what they are doing. When it comes to any type of material out there, aluminum for instance, there’s different formulae for casting and formulae for forgings and they exist to withstand the methods of the different processes. Casting metals need to flow well, not oxidize at elevated temps and cool without too much precipitation and grain boudary stresses built in. Forgings need to withstand the same but differently from being held at elevated temps longer and being beat to hell during the process.
These wheels are definitely castings but the forging process doesn’t come in until the spinning process (spin forging, not pound the hell out of it forging) and the only thing that is being spun is the actual rim, which is done with rollers that pinch and spread the cast material until you get the profile from the drop center to the sidewalls. They’re still machining the bead.
There’s nothing revolutionary about this as that’s how companies like Marchesini have been doing it with their forged magnesium wheels and that how all steel rims are made and have been for ovr 50 years. If there is anything to brag about, it would be they made a new aluminum formula for forging that also allow you to spin the rim profile without tearing the grain with microscopic cracks. I can see this allowing thinner walls with the same strength but I firmly believe they actually sacrificed some yield strength with a lower factor of safety compared to the old rims. And you still have to final machine the bead.
Will this rim be better than the cast wheel? I’m thinking just lighter but likely less yield and ultimate strength. It’s a step in the evolution of their wheels but probably there’s more to be done.
All those words and they left out the one thing that most folks would want to know– what is the weight difference between the older wheels and the newer wheels?
“Naming them Yamaha SpinForged Wheels, each boasts rims just 2 mm thick (compared to 3.5 mm with the outgoing model) and the front and rear wheels together are some 0.7 kg lighter. “
It says 0.7 kilograms for the set
All those words and they left out the one thing that most folks would want to know– what is the weight difference between the older wheels and the newer wheels?
My Yamaha 2016 R1 proved how light the wheels where. I should have purchased the wheel replacement insurance. At a track day I had the tire guy point out the flat spot on the front rim. I didn’t remember hitting anything that hard but I did ride on the New England streets between track days. They are extremely light for stock wheels but fragile.
Exactly my fear of overdoing it. In Texas, we don’t have a track anywhere that’s glass smooth, not even COTA or the Motor Speedway.
Aaaand this light weight manufacturing technology will again be wasted on motorcycles that will still weigh twice as much as the dirt bikes that the very same company makes. I have a couple of those babies right down in the shed by the lake.
I’ll bet this tech could produce some Jim Dandy beer mugs that could withstand decades of heavy partying and come right back for another refill. Ahhhh! Life in the future!
They made the wheels lighter while claiming no reduction in strength. There’s nothing more to this but you’re still looking for something to complain about.
Say it with us. Dirt bikes aren’t street bikes. Dirt bikes aren’t street bikes. Dirt bikes aren’t…
That’s pretty neat stuff. But I wonder if it is really any better than the spin-formed Mitchell wheels (Performance Machine) that I had on my GSXR 750 superbike.
The spun formed wheels had the lowest mass at rim of any wheel I ever ran, and they held 50% more air due to the deep drop center, meaning tire ran cooler and more linear compliance to bumps, I really liked those wheels. The rule back then was a pound off the rim was worth 5 lbs off the chassis.
this story has been out already for a while, the rim thickness is 2mm! thats thin!, about as thin as a scandisk card.
It sounds like cool tech but about halfway thru the press release (I’m slow) I was like “this is like a commercial and a ‘romance novel’ combined”
I agree. This press release is nauseating. Kevin Cameron wrote on this subject some time ago, it was a much easier read with much more useful info.